Графитът е често срещан неметален материал, черен, с устойчивост на високи и ниски температури, добра електрическа и топлопроводимост, добра смазваща способност и стабилни химични характеристики; добра електрическа проводимост, може да се използва като електрод в EDM. В сравнение с традиционните медни електроди, графитът има много предимства, като устойчивост на високи температури, ниска консумация на енергия и малка термична деформация. Той показва по-добра адаптивност при обработката на прецизни и сложни части и електроди с големи размери. Постепенно заменя медните електроди като електрически искри. Основният продукт на машинните електроди [1]. Освен това, износоустойчивите графитни материали могат да се използват при условия на висока скорост, висока температура и високо налягане без смазочно масло. Много оборудване широко използва графитен материал за бутални чашки, уплътнения и лагери.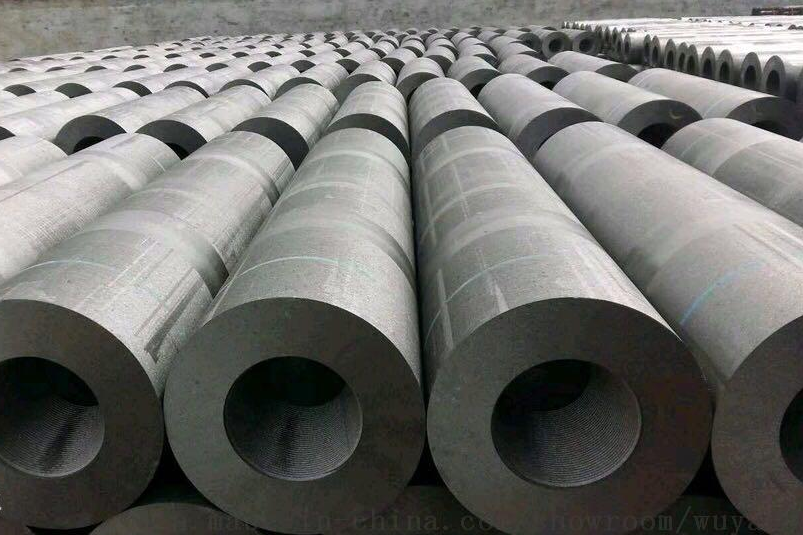
В момента графитните материали се използват широко в машиностроенето, металургията, химическата промишленост, националната отбрана и други области. Има много видове графитни части, сложна структура на частите, висока точност на размерите и изисквания за качество на повърхността. Вътрешните изследвания върху обработката на графит не са достатъчно задълбочени. Вътрешните машини за обработка на графит също са сравнително малко. Чуждестранната обработка на графит използва главно центрове за обработка на графит за високоскоростна обработка, което сега се е превърнало в основно направление за развитие на обработката на графит.
Тази статия анализира основно технологията за обработка на графит и машините за обработка от следните аспекти.
①Анализ на производителността на обработката на графит;
② Често използвани мерки за технология за обработка на графит;
③ Често използвани инструменти и параметри на рязане при обработката на графит;
Анализ на производителността на рязане на графит
Графитът е крехък материал с хетерогенна структура. Рязането с графит се постига чрез генериране на прекъснати частици стружки или прах чрез крехкото разрушаване на графитния материал. Що се отнася до механизма на рязане на графитните материали, учени в страната и чужбина са провели много изследвания. Чуждестранните учени смятат, че процесът на образуване на графитна стружка е приблизително такъв, че режещият ръб на инструмента е в контакт с детайла и върхът на инструмента се смачква, образувайки малки стружки и малки вдлъбнатини. Появява се пукнатина, която се простира до предната и долната част на върха на инструмента, образувайки вдлъбнатина, и част от детайла се счупва поради движението на инструмента, образувайки стружки. Местните учени смятат, че графитните частици са изключително фини, а режещият ръб на инструмента има голяма дъга, така че ролята на режещия ръб е подобна на екструдирането. Графитният материал в контактната зона на инструмента - детайлът се притиска от наклонената повърхност и върха на инструмента. Под налягане се получава крехко разрушаване, като по този начин се образуват стружки [3].
В процеса на рязане на графит, поради промени в посоката на рязане на заоблените ъгли или ъгли на детайла, промени в ускорението на машината, промени в посоката и ъгъла на рязане навътре и навън от инструмента, вибрации при рязане и др., върху графитния детайл се оказва определено въздействие, което води до крехкост и отчупване на ъглите, силно износване на инструмента и други проблеми. Особено при обработка на ъгли и тънки и теснооребрени графитни детайли е по-вероятно да се причинят отчупвания на ъглите и отчупване на детайла, което също се превръща в трудност при обработката на графит.
Процес на рязане на графит
Традиционните методи за обработка на графитни материали включват струговане, фрезоване, шлайфане, рязане с трион и др., но те могат да реализират обработката само на графитни детайли с прости форми и ниска прецизност. С бързото развитие и приложение на високоскоростни обработващи центрове за графит, режещи инструменти и свързани с тях поддържащи технологии, тези традиционни методи за обработка постепенно са заменени от високоскоростни технологии за обработка. Практиката показва, че поради твърдите и крехки характеристики на графита, износването на инструментите е по-сериозно по време на обработката, затова се препоръчва използването на инструменти с карбидно или диамантено покритие.
Мерки за процес на рязане
Поради особеностите на графита, за да се постигне висококачествена обработка на графитни части, трябва да се вземат съответните технологични мерки. При груба обработка на графитен материал, инструментът може директно да се подава към детайла, използвайки относително големи параметри на рязане; за да се избегне отчупване по време на довършителна обработка, често се използват инструменти с добра износоустойчивост, за да се намали количеството на рязане на инструмента. Уверете се, че стъпката на режещия инструмент е по-малка от 1/2 от диаметъра на инструмента и извършете технологични мерки, като например забавяне на обработката при обработка на двата края [4].
Необходимо е също така разумно да се организира траекторията на рязане по време на рязане. При обработка на вътрешния контур, околният контур трябва да се използва максимално, за да може силовата част на рязаната част винаги да бъде по-дебела и по-здрава и да се предотврати счупването на детайла [5]. При обработка на равнини или канали, изберете диагонално или спирално подаване, доколкото е възможно; избягвайте „островчета“ по работната повърхност на детайла и избягвайте отрязване на детайла от работната повърхност.
Освен това, методът на рязане също е важен фактор, който влияе върху рязането на графит. Вибрациите при рязане по време на фрезоване надолу са по-малки от тези при фрезоване нагоре. Дебелината на рязане на инструмента по време на фрезоване надолу се намалява от максимум до нула и няма да има отскачане, след като инструментът се вреже в детайла. Поради това, фрезоването надолу обикновено се избира за обработка на графит.
При обработка на графитни детайли със сложни структури, освен оптимизирането на технологията на обработка въз основа на горепосочените съображения, трябва да се вземат някои специални мерки според специфичните условия, за да се постигнат най-добри резултати от рязането.
Време на публикуване: 20 февруари 2021 г.